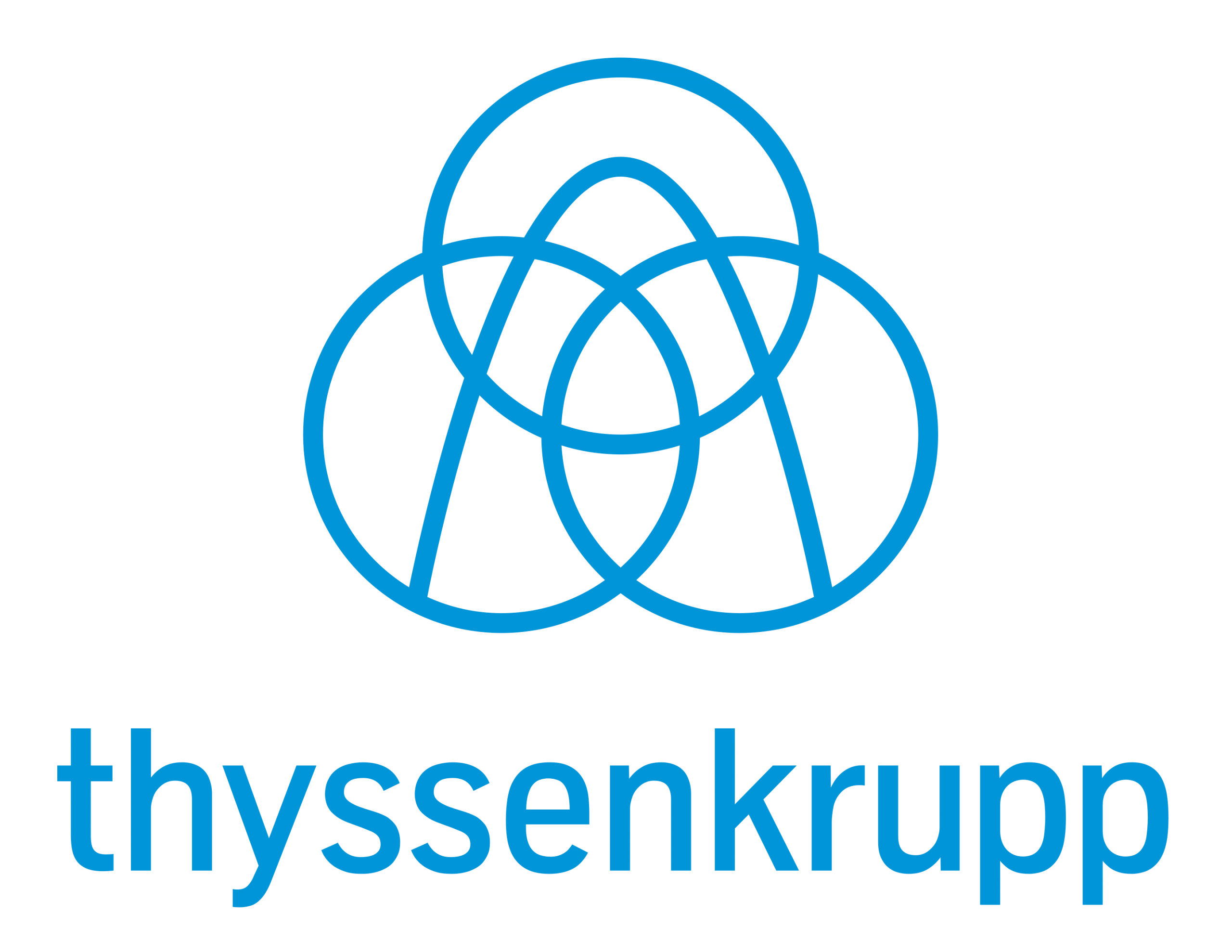
Headquartered in Essen, Thyssenkrupp AG is a listed, diversified industrial group with a focus on steel processing and Germany's largest steelmaker. The group was formed by 1999 from the merger of Friedrich Krupp AG Hoesch-Krupp with Thyssen AG. The group employs approximately 161.000 employees worldwide and has a turnover of around 43 billion euros.
Thyssen Krupp - New generation of rock crushers
When it comes to hard rock applications, mining companies rely primarily on jaw and gyratory crushers. Although these are suitable and proven for such applications, but require large installation depths.
We introduce the new eccentric roller crusher (ERC) from thyssenkrupp. The compact and rugged ERC, launched earlier this year, is suitable for both underground and underground operations.
Demitri Kokoroyanis, Product Manager, Mineral Processing, Crushing and Screening, explains that the crusher is designed for easier operation with wet, sticky material and very hard materials compared to conventional primary crushers.
“The ERC combines the ability to process hard rock material with a flat machine concept, resulting in less installation height and machine weight. The high moment of inertia of rollers and flywheels reduces power requirements and improves energy efficiency.
"In addition, the integrated pre-screening device enables fine parts to be bypassed efficiently, reduced wear and tear and increased machine capacity," he explains.
The latest generation of crusher features a fully hydraulic gap adjustment and retraction system that allows automatic gap adjustment, internal wear compensation, and release of extraneous metal or other unbreakable material.
“The ERC can also shred large hard lumps, for example the ERC 25-25 model has a roller diameter of 2500 mm and a width of 2500 mm, which can take up large lumps of up to 2000 mm x 1500 mm x 1000 mm and a degree of shredding of 1-6, ”adds Kokoroyanis.

The ERC is suitable for use above and below ground.
Cost-effective alternative to mining
Kokoroyanis goes on to explain that the main challenge for the applied crushing technology is the small footprint in the underground tunnels and chambers, which leads to special requirements for a crusher design.
Both jaw crushers and gyratory crushers, due to their large height, have the disadvantage of having to build large-volume and cost-intensive chambers for underground mining as well as for new mines where no natural deposit exists and has to be erected. The ERC has great advantages as it requires a lower bearing height.
The first prototype of the ERC 25-25 model from thyssenkrupp was tested in Germany in an open-pit application.
The crusher has undergone extensive testing for the purpose of testing to determine relevant operating parameters and process data under real conditions to demonstrate the suitability of the crusher for the ore and hard rock industries.
A hard andesite was extracted from the selected mine - a material comparable to some copper and iron ores.
The crushing plant used for the tests consisted of a feed hopper, a vibratory conveyor, the crusher with integrated primary scalping grizzly, a discharge belt, a steel structure and an aggregate.
In a trial run of more than six months, the most important process and machine parameters were determined. In all parameters, the machine met and exceeded the requirements.
Currently, the first ERC 18-14 model is commercially distributed and is in the start-up phase for mass production in an open-pit mining application in Germany.
In addition, the company is currently advising some of its sub-Saharan customers on new open-field projects.
However, as Kokoroyanis explains, thyssenkrupp is not just concentrating on delivering a cost-effective primary crusher program to its customers.
"Rather, we are closely linked to our well-known customers, as we select and tailor the best crusher for the application and ensure that all requirements for a long and safe service life of mines are met," he concluded.
Efficient comminution
thyssenkrupp minerals processing GM Wilfred Barkhuizen discusses the company's mineral processing portfolio and notes that it now includes crushing, screening, and energy generation and storage solutions, in addition to mills, high-pressure grinding rollers (HPGRs), and laboratory automation.

thyssenkrupp combines grinding and energetics to reduce overall costs. Shredding accounts for over 53% of energy use at the mine, leading to the question of how to make it more efficient and self-supporting? Not only does thyssenkrupp provide efficient shredding solutions for the mining industry, but it is also a leader in integrating renewable energy generation and storage solutions to reduce total energy costs.
crushing
The local mining customer base is probably less familiar with the destructive element of the business, but it is a strong focus focused on sub-Saharan Africa.
With decreasing ore bodies, customers need to crush and grind low-grade ores, which poses the additional challenge of crushing and grinding larger quantities. The result is that additional focus is placed on delivering products and processes that are as efficient as possible while lowering operating costs.
For the past eight years, thyssenkrupp has sold almost 50 primary gyratory crushers (largely semi-mobile plants) worldwide. The last semi-mobile primary gyratory crushers have been sold to a Zambian copper mine and have been in operation since 2015.
In addition to the need for higher throughput crushers, more and more companies are turning to semi-mobile units as they offer numerous production and cost savings benefits. Mobile crushers (including large primary gyratory crushers) can be dismantled, relocated and prepared for pre-installation elsewhere in the mine in less time.
Our products are manufactured in large, easy-to-install parts, and because they are modular, assembly and commissioning times are drastically reduced. The biggest advantage, however, is the low cost of structural preparation, which also includes the soil compaction and the support wall preparation. This significantly reduces the overall cost of breaking and adds the added value of semi-mobility.
In addition to the growing trend for semi-mobile machines, interest in underground breakers is increasing significantly. Underground mincing provides more capacity for pits, supporting high volumes and productivity.
The jaw and gyratory crushers are designed to be easily transported and mounted underground. Instead of welding assemblies, they can be screwed together, which facilitates transport to an underground location.
By and large, thyssenkrupp offers a comprehensive range of crushers, whether in fully-mobile, semi-mobile or fixed design, in the program, hammer, single toggle jaw in the standard and heavy duty range, double toggle jaw, cone crusher etc. and its unique jaw crusher It allows customers to penetrate large rocks of up to 3 m in size (ideal for quarrying). It has a significant reduction ratio and thus meets the need for high throughputs and heavy ores. The roll crushers are the largest in the industry and can achieve up to 14.000 t / h throughput.
New and innovative crushing and conveying technology in the pit
thyssenkrupp has developed a concept for a new integrated in-pit crushing and trough conveyor system that is ideally suited for open pit mining. The system is based on existing underground technology and aims to reduce or even eliminate the number of trucks that transport ore from the mine to the plant. This significantly or completely reduces diesel costs and increases productivity.
The design incorporates an 250 m high trough conveyor system that connects the pit to a higher level or to the surface and can accommodate 8 000 t / h. In discussions with various customers interested in testing the system, the differences between operating costs and conventional transport costs are realistically evaluated.
Shaping
thyssenkrupp was and is a leader in grinding technology, especially in tray-supported milling.
The shell support structure is different than any other tiller on the market. Hydrodynamic bearings on the mill shell (as opposed to spigots) provide effective load distribution, and the manufactured end walls (as opposed to castings) dramatically reduce the risks and times associated with the manufacture of roller jackets, and the unique dual pinion drive system transfers power more efficiently.
In addition to providing gearless mill drive solutions for the larger mills, the Multiflex concept drive system using 4 propulsion systems can be offered as a more economical alternative with the added reliability benefit.
One of thyssenkrupp's developments is free-welded bowls, which are becoming increasingly popular due to the larger roll diameters and the associated logistical requirements.
HPGRs
The Group is always looking for innovative solutions that enable it to develop highly effective mineral processing systems that are more energy efficient while conserving scarce water resources. In particular, we believe that our HPGRs can be used in dry fine grinding and we are intensively investigating this.
The reality is that HPGR in a finish grinding application can deliver 30 to 50% higher efficiency compared to some of the traditional loop circuits.
Quality control and automation
In all crushing and milling processes, sample analysis is one of the most important prerequisites, not only for quality assurance, but also for constantly controlling processes and adjusting them for optimum efficiency.
For this purpose we have just extended our automated laboratory systems for the South African market with further robot-supported innovations. The Polab Shuttle system gives the lab environment a unique level of flexibility as it can be fully automated and integrated into the plant control while still allowing manual operation.
The sample transfer using a mobile robot allows unlimited flexibility with regard to numerous configurations that can be extended to specific requirements. Individual modules such as a receiving station, sample preparation, input and output magazines and analyzers are interconnected by a rail system on which the robot moves. A unique safety concept allows the lab to be used by people who work with the robot, something that was not possible in the past.
Ultimately, we all strive to bring innovation to the table to make our customers' lives easier and more cost-effective.
For more information, please contact the following address:
Dr. Wilfred Barkhuizen - Managing Director: Mineral Processing, Energy & Energy
All pictures of thyssenkrupp
ISE-November 2019